Minimizing downtime and optimizing throughput in wet wipes packaging is essential for maintaining efficient production and meeting customer demand.
Manufacturers employ various strategies to achieve this goal:
- Predictive Maintenance: Implementing predictive maintenance programs allows manufacturers to anticipate equipment failures before they occur. By monitoring equipment performance and using sensors to detect signs of wear or potential issues, maintenance can be scheduled proactively during planned downtime, minimizing unplanned stoppages and maximizing equipment uptime.
- Routine Maintenance and Inspections: Conducting regular maintenance and inspections on packaging machinery helps identify and address minor issues before they escalate into major problems. Scheduled maintenance tasks, such as lubrication, cleaning, and parts replacement, ensure that equipment operates smoothly and efficiently, reducing the risk of unexpected breakdowns and downtime.
- Quick Changeover Procedures: Streamlining changeover procedures between different product variants or packaging formats reduces downtime associated with transitioning between production runs. Manufacturers implement standardized changeover protocols, use tool-less adjustment mechanisms, and invest in quick-change parts to minimize setup times and increase overall equipment efficiency (OEE).
- Continuous Improvement Initiatives: Embracing a culture of continuous improvement encourages employees to identify inefficiencies, brainstorm solutions, and implement process enhancements to optimize throughput and minimize downtime. Regular Kaizen events, lean manufacturing practices, and cross-functional teamwork foster innovation and drive operational excellence in wet wipes packaging operations.
- Real-Time Monitoring and Control Systems: Installing real-time monitoring and control systems enables manufacturers to track key performance indicators (KPIs), such as equipment speed, downtime events, and production efficiency, in real-time. By analyzing data and identifying trends, operators can proactively address bottlenecks, optimize equipment utilization, and maximize throughput.
- Training and Skills Development: Providing comprehensive training and skills development programs for packaging machine operators ensures they have the knowledge and expertise to operate equipment efficiently and troubleshoot common issues effectively. Training covers equipment operation, wet wipes packaging maintenance procedures, problem-solving techniques, and safety protocols, empowering operators to minimize downtime and maintain high levels of productivity.
- Spare Parts Inventory Management: Maintaining adequate spare parts inventory for critical components and consumables ensures rapid replacement and minimizes downtime in the event of equipment breakdowns or wear-related failures. Manufacturers implement inventory management systems to track spare parts usage, replenish stock levels, and optimize inventory turnover to support uninterrupted production.
- Contingency Planning and Risk Management: Developing contingency plans and risk mitigation strategies helps manufacturers anticipate potential disruptions and minimize their impact on production. This includes identifying alternative suppliers, establishing backup equipment arrangements, and implementing disaster recovery protocols to ensure business continuity in the face of unforeseen events.
- Collaboration with Equipment Suppliers: Building strong partnerships with equipment suppliers facilitates ongoing support, technical assistance, and access to expertise in optimizing packaging machinery performance. Manufacturers leverage supplier relationships to stay informed about equipment upgrades, maintenance best practices, and emerging technologies that can enhance throughput and minimize downtime.
- Data-Driven Decision Making: Utilizing data analytics and performance metrics to inform decision-making enables manufacturers to identify opportunities for improvement, prioritize optimization efforts, and track progress towards throughput targets. By leveraging data insights, manufacturers can make informed decisions to streamline processes, enhance efficiency, and minimize downtime in wet wipes packaging operations.
By implementing these strategies, manufacturers can minimize downtime and optimize throughput in wet wipes packaging, ensuring efficient production, reduced costs, and enhanced competitiveness in the market.
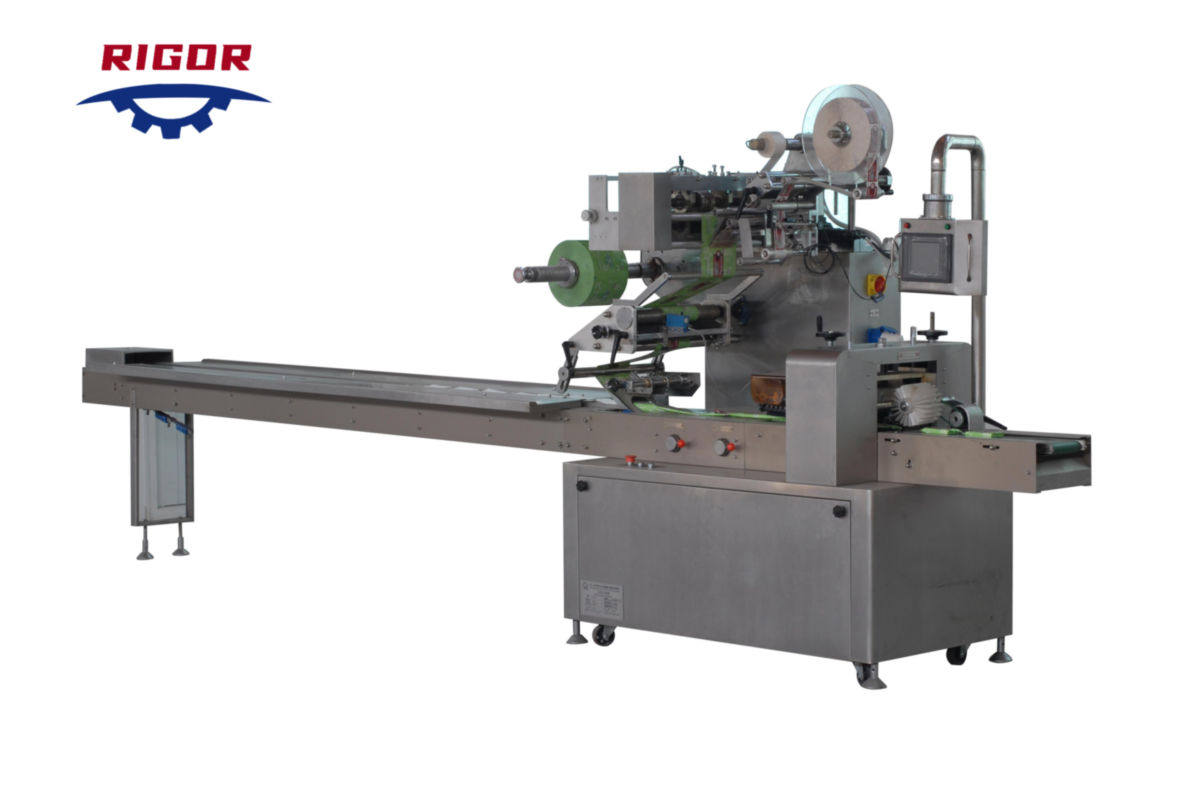